Composants de systèmes à vapeur
Sixième module
Dans ce module, nous présentons les principaux composants des systèmes à vapeur.
Le volume horaire est d'environ 2 h de travail.
Thème 1 : Générateurs de vapeur
Générateurs de vapeur
On appelle générateurs de vapeur (GV) des chaudières où la chaleur n'est pas fournie par une combustion.
La plupart des GV sont des variantes des chaudières à tube d'eau. Dans celles-ci, l'eau circule à travers un réseau de tubes, par convection naturelle ou forcée, entre deux ballons placés l'un au-dessus de l'autre (à l'exception des chaudières supercritiques). La flamme se développe dans un foyer tapissé de tubes qui absorbent le rayonnement. Un second faisceau de tubes reçoit sa chaleur des fumées par convection. L'eau monte dans les tubes soumis au rayonnement, et descend par le faisceau de convection.
Les différences essentielles entre elles et un GV proviennent d'une part de ce que les niveaux de température dans les GV sont généralement beaucoup plus faibles que ceux que l'on atteint dans une chaudière, et de ce que l'échange de chaleur se fait uniquement par voie convective.
On appelle GVR ou générateur de vapeur récupérateur un GV dont la source chaude correspond à un flux d'effluents qui se refroidit. Leur comportement s'apparente à ceux des GV nucléaires, ce qui explique qu'on en parle ici.
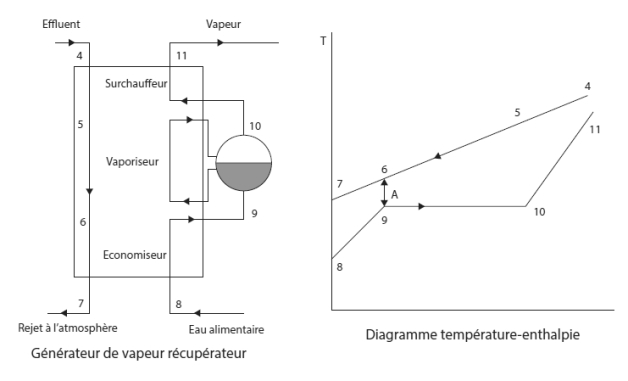
On voit apparaître sur le diagramme enthalpie-température de la figure ci-dessus, au niveau du point 6, un minimum A dans l'écart de température entre les deux fluides, appelé pincement. Ce point joue un rôle fondamental dans le dimensionnement du GVR, puisqu'il représente le plus faible écart de température dans l'installation. Pour réduire le coût des équipements, il est préférable que le pincement ne soit pas trop faible. En revanche, l'optimisation thermodynamique du système complet demande qu'il soit le plus réduit possible.
Une attention particulière doit donc être apportée à la conception du GVR au niveau de ce pincement, qui doit être supérieur à une valeur minimale de l'ordre de 10 à 15 °C, faute de quoi la vaporisation ne peut se faire à la température désirée.
Remarque importante
Compte tenu des faibles écarts de température entre les circuits primaire et secondaire des réacteurs du type REP, la nécessité de transférer une puissance importante interdit en pratique de réaliser toute surchauffe dans leurs GV, car les coefficients d'échange entre le liquide primaire et la vapeur surchauffée seraient trop faibles. Cette contrainte existe aussi dans les réacteurs à eau bouillante REB, afin d'éviter tout risque de surchauffe locale du cœur.
Thème 2 : Dégazeur, bâche alimentaire
Le schéma de la figure ci-dessous montre les différents éléments constitutifs d'un réseau de vapeur :
l'alimentation en eau : l'eau brute arrive en 1, en bas à droite. Cette eau doit être traitée pour éviter l'encrassement et la corrosion du réseau. En 2, l'eau traitée est introduite dans la bâche alimentaire, où elle se mélange aux condensats qui reviennent sur le réseau de retour, après utilisation par les différents procédés ou équipements de chauffage ou de production de force motrice ;
le dégazage de l'eau : la bâche alimentaire joue par ailleurs un rôle fondamental : dégazer l'eau. Le dégazage permet d'éliminer les différents gaz dissous dans l'eau, en particulier le gaz carbonique et l'oxygène très corrosif dans la chaudière et les canalisations de retour. De plus, la présence d'air ou d'incondensables a pour effet de limiter les coefficients d'échange par formation d'un film d'air qui s'oppose au transfert thermique, ce qui augmente l'écart entre les températures de condensation et du fluide de refroidissement ;
le générateur de vapeur : en sortie de dégazeur en 3, l'eau est mise sous pression par une pompe alimentaire, puis dirigée vers le générateur de vapeur, où elle est chauffée à l'état liquide dans l'économiseur, vaporisée dans le vaporiseur, puis surchauffée. Des séparateurs assurent le séchage de la vapeur pour éviter que de l'eau liquide soit emportée dans le réseau vapeur. On appelle primage ce phénomène d'entraînement qui peut parfois se produire malgré les précautions prises. Les causes peuvent être soit un mauvais traitement de l'eau, qui conduit à une concentration en sels trop élevée, soit un appel brutal de vapeur, soit une erreur de conception. Bien que les termes de chaudière et de générateur de vapeur puissent être considérés comme synonymes, nous réserverons le second pour désigner des appareils fonctionnant sans combustion, comme les réacteurs nucléaires ;
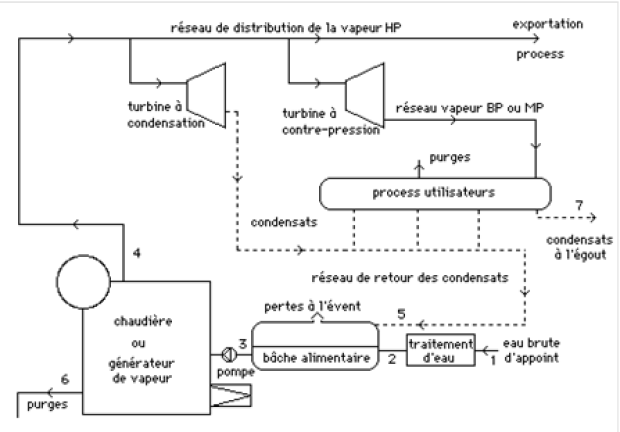
les purges de déconcentration : sans elles, les sels dissous dans l'eau ne se vaporisant pas, leur concentration augmenterait au-delà des valeurs acceptables (corrosion) du fait de l'introduction d'eau d'appoint en 1 ;
les postes d'utilisation de la vapeur : la vapeur surchauffée sort en 4 de la chaudière et est acheminée vers les différents postes d'utilisation. Comme indiqué, il est fréquent que le réseau de vapeur se compose de plusieurs sous-réseaux, à haute pression (> 40 bars), moyenne pression (environ 20 bars) et basse pression (4 bars), en fonction des besoins des utilisateurs. Une partie de la vapeur peut aussi être exportée vers une autre zone de l'usine ou des clients extérieurs. On a représenté sur le schéma une turbine, et différents procédés ;
le retour des condensats : après usage, la vapeur est détendue, généralement à la pression atmosphérique, et les condensats sont redirigés vers la bâche alimentaire (5), si leur qualité le permet, sinon évacués vers l'égout (7). De surcroît, des purges sont pratiquées pour des raisons diverses au niveau des postes d'utilisation. Toutes ces pertes expliquent la nécessité d'apporter un appoint d'eau.
Bâche alimentaire
La bâche alimentaire, également connue sous le nom de réservoir d'eau d'alimentation, est un composant clé du système d'alimentation en eau d'une centrale à vapeur.
Elle agit comme un réservoir de stockage pour l'eau d'alimentation de la chaudière, et permet d'accumuler une réserve d'eau prête à être utilisée lorsque cela est nécessaire, ce qui est particulièrement important pour les centrales à vapeur qui doivent répondre rapidement aux variations de la demande.
La bâche alimentaire est conçue pour maintenir la pression et la température de l'eau d'alimentation à des niveaux appropriés pour la production de vapeur.
Elle est souvent équipée de systèmes de traitement de l'eau pour éliminer les impuretés et les gaz dissous qui pourraient compromettre le fonctionnement de la chaudière. Cela comprend généralement des filtres, des dégazeurs et des dispositifs de traitement chimique pour assurer la qualité de l'eau d'alimentation.
En résumé, la bâche alimentaire joue un rôle essentiel dans le processus de production d'électricité d'une centrale à vapeur en stockant, régulant et fournissant de l'eau d'alimentation de qualité à la chaudière. Elle contribue à garantir l'efficacité, la fiabilité et la sécurité du système dans son ensemble.
Dégazage de l'eau
Il peut être fait sous forme chimique ou thermique.
Dégazage chimique
Le réactif utilisé pour extraire l'oxygène est l'hydrazine (N2H4) :
N2H4 + 02 --> 2 H2O + N2
L'excédent d'hydrazine se décompose quant à lui dans la chaudière en azote et en ammoniac :
3 N2 H4 --> 4 NH3 + N2
L'ammoniac emporté par la vapeur contribue à relever le pH des condensats, et se combine avec le gaz carbonique pour produire du bicarbonate d'ammoniac. En cas de dégazage chimique, il faut proscrire l'utilisation du cuivre dans le réseau de retour des condensats.
L'utilisation du dégazage chimique est limitée aux installations de petite taille, ou encore comme complément à un dégazage thermique.
Dégazage thermique
D'après la loi de Henry, la solubilité d'un gaz est proportionnelle à sa pression partielle dans la phase gazeuse, le coefficient de proportionnalité φ étant fonction de la température. Dans le cas de l'oxygène, φ passe par un minimum autour de 100 °C, et varie peu entre 75 et 125 °C.
Le dégazage est assuré en portant à ébullition l'eau alimentaire, ce qui permet de diminuer la pression partielle de O2 et CO2. Les gaz libérés sont alors rejetés dans l'atmosphère, soit par décharge à travers un évent si la pression du dégazeur est supérieure à la pression atmosphérique, soit par extraction par une pompe à vide si elle est inférieure.
Le principal inconvénient du dégazage à dépression est qu'en cas de fuite, il y a entrée d'air, ce qui est exactement contraire au but recherché. C'est pourquoi les dégazeurs opèrent généralement en légère surpression, à des températures voisines de 110 à 120 °C, et pouvant aller jusqu'à 150 °C. La température de retour des condensats étant comprise entre 50 et 80 °C, il est alors nécessaire d'apporter un complément de chaleur à la bâche alimentaire. En sortie de dégazeur, la teneur en oxygène de l'eau alimentaire est comprise entre 0,007 et 0,02 mg/l.
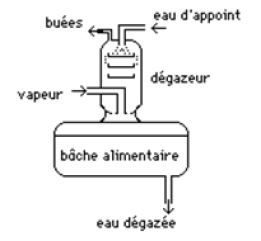
Purges de déconcentration
Afin de maintenir la concentration en chaudière des sels dans les limites recommandées par les constructeurs, il est nécessaire de pratiquer des purges, continues ou intermittentes, qui sont fonction d'une part de la qualité de l'eau d'appoint, et d'autre part de la proportion de retour des condensats. On les appelle purges de déconcentration.
Elles sont caractérisées par le taux de purge D/V, rapport des purges de déconcentration à la vapeur produite. Sc étant la concentration limite en chaudière, et Sb la concentration moyenne dans la bâche alimentaire, un bilan massique sur les sels entrant dans et sortant de la chaudière (D Sc - V Sb = 0 à l'équilibre) montre aisément que D/V est donné par la formule :
D/V = Sb/Sc . Selon les cas, Sc et Sb sont exprimées en mg/l ou en °f (degré français).
On calcule successivement, pour les différentes catégories de sels, les valeurs de D/V à respecter, et on retient la plus élevée.
Le taux de purge D/V peut parfois atteindre des valeurs importantes, notamment dans les chaudières à haute pression, où les concentrations limites Sc sont faibles. Il peut en résulter une perte énergétique non négligeable si l'enthalpie résiduelle des purges n'est pas récupérée, par exemple pour fournir l'énergie nécessaire au bon fonctionnement du dégazeur. Pour cela, il est possible de détendre les purges dans un ballon et d'envoyer la vapeur de revaporisation dans la bâche alimentaire ou le dégazeur. La chaleur sensible des purges liquides détendues peut aussi éventuellement être récupérée dans un économiseur.
Thème 3 : Turbines à vapeur
L'agencement général d'une turbine est donné dans la figure ci-dessous. Un stator suivi d'un rotor sont traversés en série par de la vapeur à haute pression et température. Le stator est constitué de tuyères de guidage qui accélèrent le fluide, tandis que la roue (rotor) convertit en énergie mécanique au moins une partie de l'enthalpie disponible. U est la vitesse tangentielle du rotor.
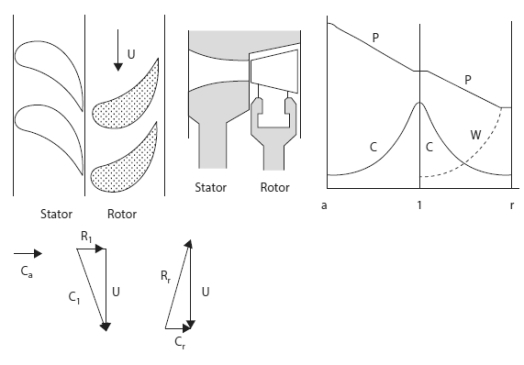
Dans une turbine, l'évolution du fluide est une détente. Les équations d'écoulement compressibles que nous ne développerons pas ici indiquent que pour un régime subsonique, la section de la veine devrait diminuer, et la vitesse augmenter. Cette évolution se fait en deux étapes (figure ci-dessus) : dans le stator, la vitesse absolue C augmente, tandis que dans le rouet la vitesse relative W augmente, et la vitesse absolue C diminue.
Pour une vitesse de rotation N donnée, la caractéristique des performances d'une turbine a l'allure de la figure ci-dessous, où un groupe de variables appelées débit massique corrigé proportionnel au nombre de Mach dans l'écoulement apparaît en ordonnée, et l'inverse du taux de détente en l'abscisse. L'indice 0 se rapporte aux conditions d'entrée de la turbine.
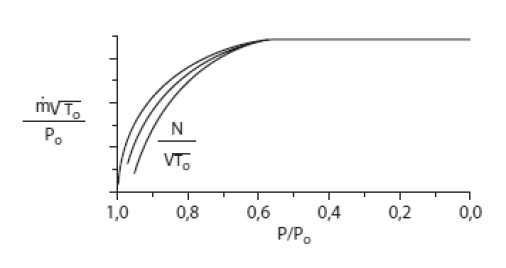
Différents types de turbines à vapeur
En fonction de leur utilisation, on distingue quatre grandes catégories de turbines (figure ci-dessous) :
les turbines à condensation, dans lesquelles la vapeur est complètement détendue jusqu'à une pression voisine de 0,02 à 0,04 bar, puis liquéfiée dans un condenseur refroidi soit par l'air ambiant, soit par de l'eau. Ce type de turbine est surtout utilisé dans les installations de production de force motrice ;
les turbines à contre-pression, dans lesquelles la vapeur est détendue de la pression HP (> 40 bar) jusqu'à une pression BP (de l'ordre de 4 bar). Ce type de turbine permet de produire de la puissance mécanique ou de l'électricité grâce aux hautes température et pression que l'on peut obtenir dans une chaudière, tout en utilisant l'enthalpie résiduelle pour des procédés divers ;
les turbines à soutirage et condensation, dans lesquelles la vapeur subit une détente partielle jusqu'à une moyenne pression (environ 20 bar) dans un corps haute pression. Une partie est dirigée vers un réseau d'utilisation, tandis que le reste de la vapeur est détendu dans un corps basse pression, comme dans une turbine à condensation. Ce type de turbine trouve un champ d'application important dans les usines de cogénération dont les demandes de chaleur sont susceptibles de varier fortement au cours du temps ;
les turbines à soutirage et contre-pression, dont la vapeur s'échappe à basse pression dans un réseau BP au lieu d'être condensée.
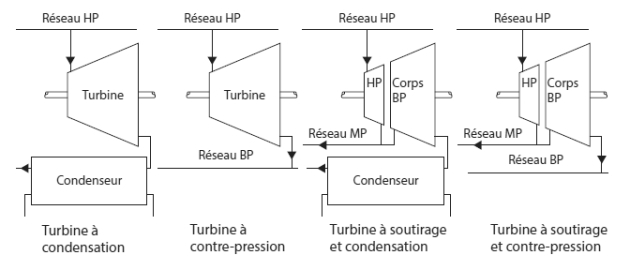
Cette page du portail Thermoptim-Unit présente les turbines.
Texte à trous
Ce texte à trous vous permettra de vérifier votre connaissance des différents types de turbines à vapeur.
Thème 4 : Éjecteurs
Un éjecteur (figure ci-dessous) reçoit en entrée deux fluides généralement gazeux, mais qui peuvent aussi être liquides ou diphasiques :
le fluide à haute pression, appelé fluide moteur ou primaire ;
le fluide à basse pression, appelé fluide secondaire ou entraîné.
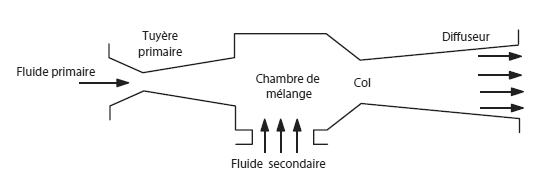
Le fluide moteur est accéléré dans un convergent-divergent (a sur la figure), créant une baisse de pression dans la zone de mélange (b sur la figure), ce qui a pour effet d'aspirer le fluide secondaire. Les deux fluides sont alors mélangés et une onde de choc peut prendre place dans la fin de cette zone. Il en résulte une augmentation de la pression du mélange et une baisse de sa vitesse, qui devient subsonique. Le diffuseur (c sur la figure) permet de convertir la vitesse résiduelle en augmentation de pression.
L'éjecteur réalise ainsi une compression du fluide secondaire au prix d'une baisse d'enthalpie du fluide primaire. C'est la raison pour laquelle on appelle souvent thermocompresseur un éjecteur, et on parle de thermocompression. Nous en verrons un exemple dans le module sur le dessalement.
Les éjecteurs sont couramment utilisés pour extraire les incondensables des condenseurs des cycles à vapeur. La fiche-guide FG21 vous permettra d'approfondir cette question si elle vous intéresse particulièrement.
Une présentation complète des éjecteurs et de la manière dont ils peuvent être modélisés est donnée dans cette page du portail.
Thème 5 : Tours de refroidissement
Les performances des installations à vapeur fonctionnant en circuit fermé sont très sensibles aux conditions dans lesquelles la vapeur peut être condensée. En effet, un condenseur est un échangeur d'un type particulier, à changement de phase, dont l'équilibre thermique détermine la température de condensation de la vapeur, et donc sa pression de condensation.
Une tour de refroidissement est un échangeur d'un type particulier très utilisé dans les centrales nucléaires de grande capacité, qui permet de rejeter de la chaleur dans l'air environnant sous forme à la fois de chaleur sensible et de chaleur latente du fait de l'augmentation de son humidité. En opérant de la sorte, il est possible de refroidir un fluide jusqu'à une température supérieure de quelques degrés à la température humide de l'air ambiant (et donc éventuellement inférieure à sa température sèche), ceci au prix d'une quantité d'eau consommée de l'ordre de 5 % de celle que demanderait un refroidissement à eau. Tant sur le plan économique qu'environnemental, les tours de refroidissement sont des systèmes très intéressants, notamment en climat chaud et sec.
On distingue deux grandes catégories de tours de refroidissement, celles dites à contact direct ou à cycle ouvert, et celles dites à contact indirect ou à cycle fermé.
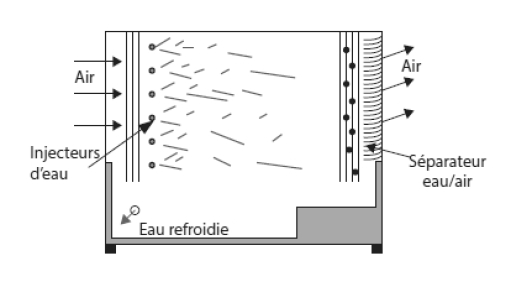
Dans une tour à contact direct, l'eau chaude à refroidir est mise en contact avec l'air ambiant, soit par pulvérisation en fines gouttelettes, soit par ruissellement le long de surfaces d'écoulement. Les deux fluides étant en contact, de la chaleur est échangée par convection, et une partie de l'eau se vaporise, en augmentant ainsi l'humidité de l'air. Si celui-ci n'est pas saturé, il commence par se refroidir de manière quasiment adiabatique, avant de s'échauffer le long de la courbe de saturation. L'eau peut donc ressortir à une température inférieure à celle de l'air ambiant
Une tour à contact indirect met en jeu deux circuits, dits externe et interne. Dans ce dernier, le fluide à refroidir, qui peut être quelconque, reste confiné dans un faisceau de tubes autour desquels ruisselle l'eau de refroidissement du circuit externe, qui se réchauffe à son contact, puis se refroidit par échange avec l'air ambiant selon le même mécanisme que dans une tour à contact direct.
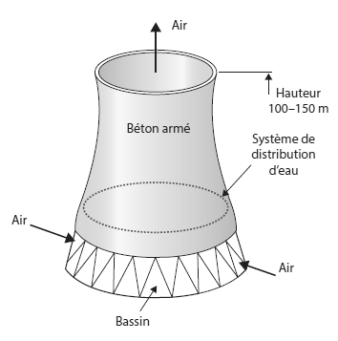
Du fait de l'évaporation d'une partie de l'eau, la concentration des sels dissous et celle des impuretés, notamment biologiques, est amenée à augmenter. On doit donc d'une part procéder à des purges de déconcentration, et d'autre part veiller à éviter tout risque de propagation de légionellose.
Modèle phénoménologique
La modélisation théorique des tours de refroidissement est assez complexe compte tenu de la multiplicité des transferts qui y prennent place.
Les hypothèses généralement faites, dues à Merkel, sont les suivantes :
l'air sortant de la tour est quasiment saturé
le film interstitiel est de l'air saturé d'humidité, à la température de l'eau
le nombre de Lewis est égal à 1
la résistance thermique côté liquide est négligée devant celle côté air
Elles permettent d'aboutir à un modèle dans lequel la principale caractéristique de la tour est un Nombre d'Unités de Transfert NUTm, résultat de l'intégration de l'équation suivante.
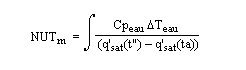
Il s'agit d'un indicateur représentatif de la difficulté qu'il y a à effectuer le transfert thermique dans la tour de refroidissement. Incorporant des phénomènes couplés d'échange d'énergie et de masse complexes, et dépendant de la technologie mise en œuvre, il n'est pas possible d'en donner une expression simple.
On appelle " approche" (en anglais " approach") le pincement[1] de la tour, c'est-à-dire l'écart entre la température de sortie de l'eau et la température humide de l'air ambiant et " refroidissement" (en anglais " range") la valeur de la variation de température de l'eau.
NUT est généralement fonction de quatre variables :
le rapport du débit massique d'eau au débit massique d'air
la température humide de l'air à l'entrée de la tour
soit les deux températures de l'eau Tee et Tes
soit le refroidissement (Tee - Tes) et l'approche (Tes - T'ae).
Modèles de comportement
De nombreux auteurs se sont intéressés à la modélisation des tours de refroidissement, et ont cherché des expressions de NUT qui soient à la fois faciles à calculer et en accord avec les résultats expérimentaux. Étant donné qu'il s'agit avant tout d'un indicateur de performance, il n'est pas en soi rédhibitoire qu'il existe une part d'arbitraire dans sa définition, dans la mesure cependant où les conventions retenues sont bien précisées.
Modèle de Merkel
L'expérience montre que, lorsque l'on modifie les quatre variables d'entrée d'une tour de refroidissement donnée, NUTm prend des valeurs diverses, qui suivent une loi de comportement du type suivant, n et m ayant des valeurs négatives comprises entre -1,1 et -0,35, et C étant compris entre 1 et 2,5 environ. C et n ou m sont appelés les coefficients de la tour.
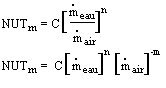
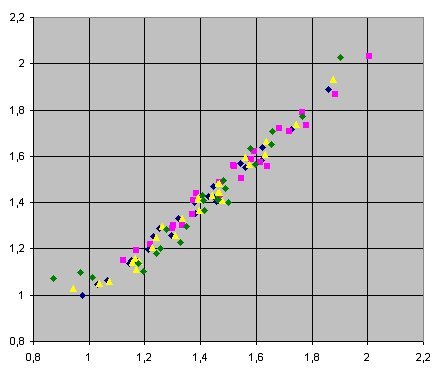
Correspondance entre NUTm constructeur et corrélation
Cette figure montre la très bonne correspondance qui existe entre les valeurs de NUTm calculées pour le même modèle de tour de refroidissement (F1221 de la société Marley ) avec quatre motorisations de ventilateur différentes (40, 50, 60 et 70 hp).
Exemple d'utilisation d'une tour de refroidissement
Nous allons utiliser le modèle présenté dans cette fiche thématique pour étudier l'intérêt d'utiliser une tour de refroidissement à la place d'un aérocondenseur sec pour une centrale à vapeur.
Nous repartons de l'exemple présenté à la fin du cinquième module, où nous avons paramétré un tel échangeur de chaleur.
Le pincement dans l'aérocondenseur était de 11 K, du fait que l'un des deux fluides était un gaz. Dans le nouveau condenseur, le pincement peut être réduit à 7 K du fait de son remplacement pas de l'eau (voir module 8 pour davantage d'explications). De plus, l'air ambiant à 10 °C et 50 % d'humidité relative peut être refroidi jusqu'à 8,44 °C, et l'eau de refroidissement à l'entrée du condenseur jusqu'à 7 °C.
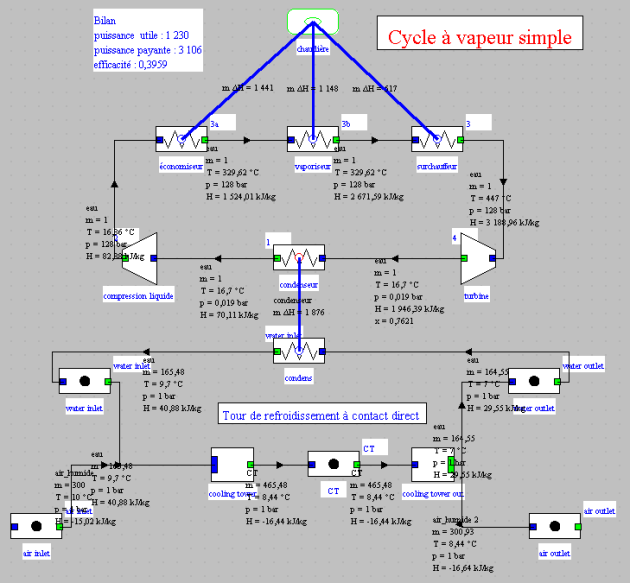
L'écran du composant tour de refroidissement est donné ci-dessous. On désire ici refroidir 165,5kg/s d'eau de 9,7 °C à 7 °C. Avec un débit de 300 kg/s d'air ambiant à 10 °C et d'humidité relative égale à 0,5, la température de l'air sortant est de 8,44 °C et 933 g/s d'eau sont évaporés. La puissance de la tour est de 1876 kW.
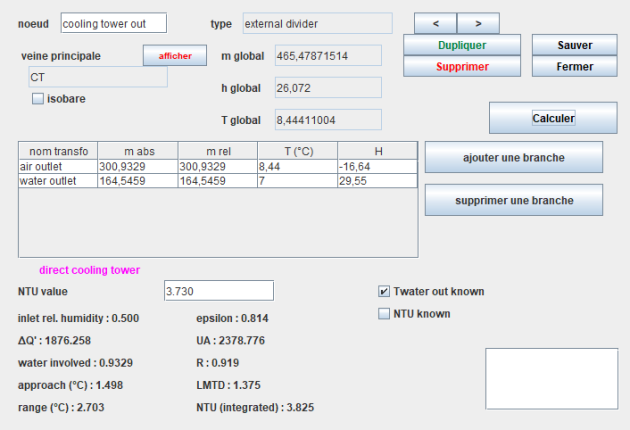
Le paramétrage de la tour a été fait de la manière suivante (figure ci-dessus) : on fixe T et ε pour l'air en entrée (ici 10 °C et 50 % d'humidité relative) et Teau en entrée (ici 9,7 °C). Le débit d'eau (165,5 kg/s) est déterminé par l'équilibrage du condenseur qui fixe aussi la puissance à extraire ΔH et le niveau de température de sortie de l'eau. Le débit d'air doit être suffisant pour que le problème ait une solution. La valeur trouvée lors du dimensionnement de l'aérocondenseur fournit un ordre de grandeur.
La diminution des pincements dans le condenseur avec tour de refroidissement permet de condenser l'eau du cycle à une température et donc une pression plus basses qu'avec l'aérocondenseur sec.
Il en résulte un rapport de détente plus élevé et donc une production accrue de puissance mécanique (1230 kW au lieu de 1174 avec l'aérocondenseur sec, soit un gain de 4,8 %). L'eau sortant du condenseur étant à température plus basse, la puissance de la chaudière augmente légèrement, mais le rendement est lui aussi un peu plus élevé (39,59 % au lieu de 38,33 %, soit un gain de 3,3 %).
En réduisant l'écart de température entre le cycle et sa source froide, la tour de refroidissement améliore les performances de l'installation.
Un deuxième exemple est à votre disposition. Il montre les gains apportés par une tour de refroidissement pour extraire la chaleur du condenseur d'une machine de réfrigération. Il est présenté dans la fiche guide n° 6.
Connaissances acquises
Grâce à ce programme, à la fin du module, vous saurez :
identifier les principaux composants qui sont mis en œuvre dans un réseau de vapeur
expliquer quels sont les différents types de turbines à vapeur
comment fonctionne un éjecteur
analyser le fonctionnement d'une tour de refroidissement